In the integrated design of high-pressure cleaning and vacuuming, the commonly used energy-saving technologies mainly include the following aspects:
1. Frequency conversion technology
Frequency conversion technology is one of the commonly used energy-saving means in integrated high-pressure cleaning and vacuuming equipment. By controlling the speed of the high-pressure water pump and the vacuum fan through the frequency converter, the equipment can automatically adjust the power according to the actual operation needs to avoid unnecessary energy waste. For example, in lightly polluted sections or low-load operations, the equipment can automatically reduce the power, thereby significantly reducing energy consumption.
2. Intelligent control system
The intelligent control system can automatically adjust the operation mode according to the degree of road pollution and the operating environment. For example, by monitoring the dirt on the road through sensors, the equipment can automatically determine whether high-pressure cleaning or vacuuming is required, and adjust the corresponding power and flow. This intelligent control method not only improves the operating efficiency, but also reduces the energy waste caused by excessive cleaning or vacuuming.
3. Optimized water and gas circuit design
The integrated equipment reduces energy loss by optimizing the water and gas circuit design. For example, the use of efficient nozzle design and reasonable pipeline layout can ensure the efficient use of high-pressure water flow, reduce water waste and power consumption. At the same time, the optimized air path design can improve the dust collection efficiency and reduce the energy consumption of the fan.
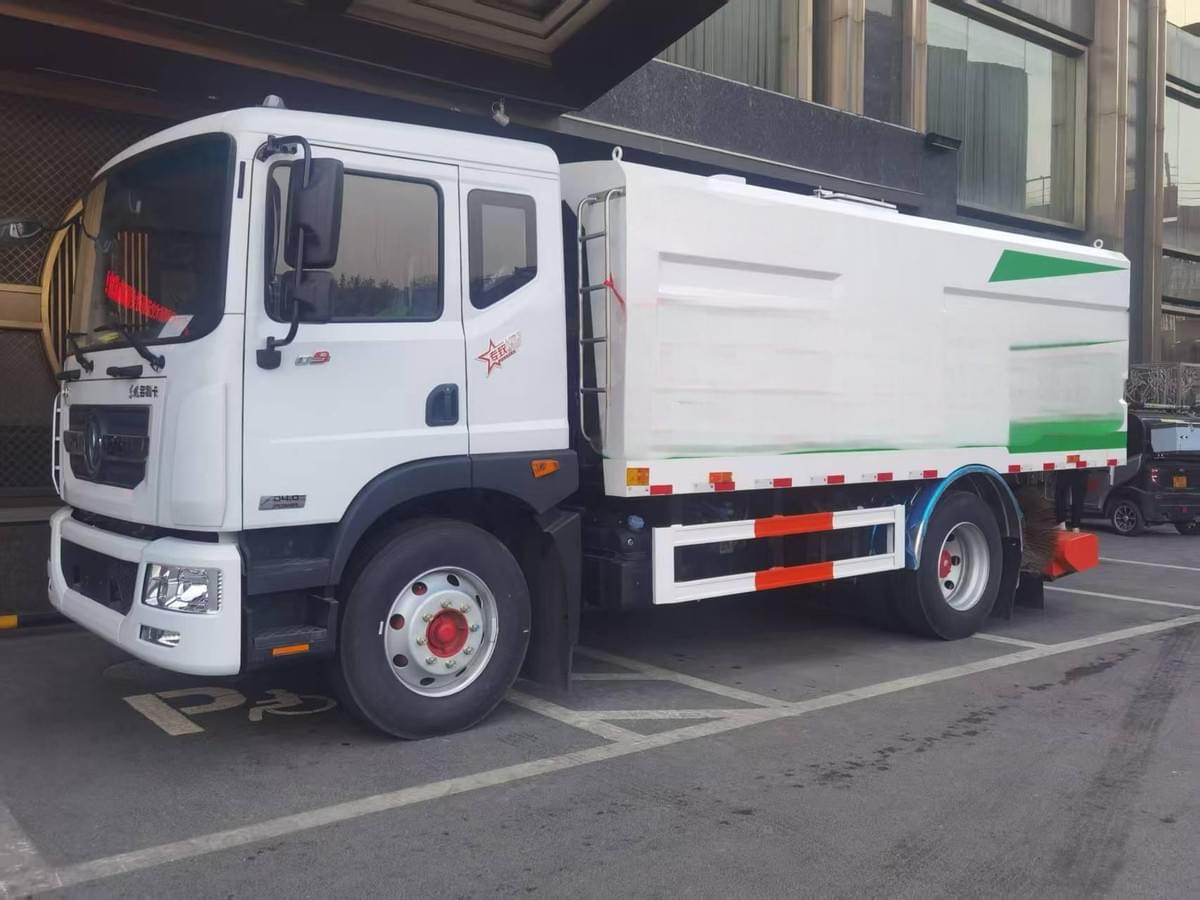
4. Energy recovery system
Some high-pressure cleaning and dust collection integrated equipment are equipped with energy recovery systems. For example, during the operation of the equipment, by recovering part of the energy (such as the residual pressure of the high-pressure water flow or the residual heat of the fan) and reusing it, energy consumption can be further reduced.
5. Low-energy motors and fans
The use of high-efficiency and energy-saving motors and fans is an important measure to reduce energy consumption. These devices optimize the design of motors and fans to improve their energy efficiency ratio, thereby significantly reducing energy consumption while ensuring equipment performance.
6. Precise operation mode switching
Integrated equipment usually has multiple operation modes, such as high-pressure cleaning mode, dust collection mode and combined mode. Through precise mode switching, the equipment can select the most energy-saving mode according to different operation needs, avoid unnecessary function operation, and thus reduce energy waste.
7. Lightweight design
By optimizing the structural design of the equipment and reducing the weight of the equipment, the energy consumption during the operation of the equipment can be reduced. For example, the use of high-strength lightweight materials to manufacture the shell and components of the equipment not only improves the durability of the equipment, but also reduces the energy consumption caused by the weight of the equipment.
8. Low noise design
Low noise design can not only reduce noise pollution to the environment, but also improve the operating efficiency of the equipment. For example, by optimizing the operating parameters of the fan and water pump, the noise during the operation of the equipment can be reduced, and the additional energy consumption due to noise control can also be reduced.
The application of these energy-saving technologies has enabled the high-pressure cleaning and vacuuming integrated equipment to significantly reduce energy consumption while improving operating efficiency, which meets the requirements of modern environmental protection and sustainable development.